精準(zhǔn)回轉(zhuǎn)工作臺(tái)五軸聯(lián)動(dòng)機(jī)床有限元結(jié)構(gòu)分析
航空發(fā)動(dòng)機(jī)作為飛機(jī)的動(dòng)力裝置,是飛機(jī)的“心臟”,按照不同的使用要求應(yīng)具有安全性、可靠、綠色、環(huán)保、長(zhǎng)壽命、易維護(hù)等特點(diǎn),因此航空發(fā)動(dòng)機(jī)零件制造對(duì)加工設(shè)備要求較高,不同材料、不同結(jié)構(gòu)的發(fā)動(dòng)機(jī)零件需要的加工設(shè)備不同,總體上對(duì)加工設(shè)備的要求為高精度、高剛性、高穩(wěn)定性、多功能和易維護(hù)…。隨著數(shù)字化制造技術(shù)、信息化技術(shù)的發(fā)展,數(shù)控深孔鉆加工機(jī)床廣泛應(yīng)用于航空制造領(lǐng)域,選擇加工航空零件的數(shù)控機(jī)床設(shè)備,首先要考慮加工零件的結(jié)構(gòu)特點(diǎn)、尺寸精度要求和零件材料特性。葉盤、葉片加工設(shè)備通常采用精準(zhǔn)五軸聯(lián)動(dòng)加工中心,能夠在一臺(tái)精準(zhǔn)五軸聯(lián)動(dòng)加工中心上完成葉片型面和榫頭的全部加工任務(wù)[2-31;剞D(zhuǎn)工作臺(tái)數(shù)控五軸聯(lián)動(dòng)機(jī)床是用于加工飛機(jī)發(fā)動(dòng)機(jī)葉片的關(guān)鍵設(shè)備,在機(jī)床的設(shè)計(jì)過(guò)程中,有必要采用有限元分析技術(shù)對(duì)機(jī)床整體結(jié)構(gòu)進(jìn)行靜態(tài)和動(dòng)態(tài)性能計(jì)算,保證機(jī)床加工葉片的高精度和穩(wěn)定性。
1、有限元模型建立
根據(jù)機(jī)床各大件結(jié)構(gòu)情況,采用殼結(jié)構(gòu)(Shell model)和實(shí)體結(jié)構(gòu)(Solid model)混合建模方式建立整機(jī)的有限元模型,對(duì)機(jī)床進(jìn)行結(jié)構(gòu)靜力學(xué)和動(dòng)力學(xué)計(jì)算[410 CAE建模過(guò)程完全采用ANSYS命令流控制,這樣既可以提高計(jì)算精度,同時(shí)又能采用批處理方式處理多種分析工況,提高工作效率。立柱和底座是由薄板焊接成的結(jié)構(gòu)件,所以在有限元建模時(shí)用二維板殼單元建模;主軸頭為復(fù)雜的鑄造結(jié)構(gòu)件,采用三維實(shí)體單元處理。為提高計(jì)算精度,在需要建立位移協(xié)調(diào)關(guān)系的導(dǎo)軌接觸部位的實(shí)體部分用六面體單元?jiǎng)澐志W(wǎng)格,圖1為參數(shù)化后的立柱殼結(jié)構(gòu)模型與有限元網(wǎng)格。
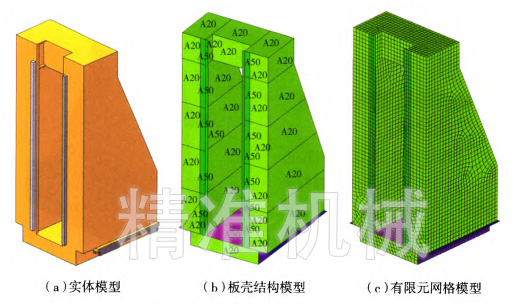
將立柱、底座、主軸頭三獨(dú)立部件在CAE環(huán)境下按照機(jī)床裝配關(guān)系進(jìn)行組裝,立柱與底座、主軸頭與立柱之間的結(jié)合面采用彈性單元進(jìn)行連接,滑塊和導(dǎo)軌均簡(jiǎn)化為彈性單元,之間建立位移耦合連接關(guān)系,以此方式完成機(jī)床整體有限元模型的集成(圖2),模擬立柱一底座、立柱一主軸頭之間結(jié)合面約束關(guān)系,實(shí)現(xiàn)作用力的準(zhǔn)確傳遞。
ANSYS提供APDL(ANSYS Parametric Design Language)命令流編程方式編寫分析文件,借助APDL,可實(shí)現(xiàn)結(jié)構(gòu)快速建模、參數(shù)化批量化有限元計(jì)算;并適應(yīng)結(jié)構(gòu)的變化,通過(guò)修改其中的參數(shù),快速生成新的結(jié)構(gòu),之后進(jìn)行網(wǎng)格劃分、加載、求解,完成結(jié)構(gòu)的再分析,通過(guò)綜合比較這些方案的分析結(jié)果,就能發(fā)現(xiàn)結(jié)構(gòu)改進(jìn)的方向。如深孔鉆立柱參數(shù)可分為形狀參數(shù)和厚度參數(shù),形狀參數(shù)定義了結(jié)構(gòu)的拓?fù)渫庥^,厚度參數(shù)用來(lái)給面單元賦值。圖3為通過(guò)參數(shù)輸入建立的3種立柱模型。
2、機(jī)床靜載荷條件下的性能分析
計(jì)算采用4種工況進(jìn)行,沿x、y、z三加工方向分別施加最大推力,定義為工況l、2、3;最后三方向綜合施加最大推力,定義為工況4。應(yīng)用工況1、2、3的
計(jì)算結(jié)果,可計(jì)算出機(jī)床沿x、y、z各加工方向的剛度,由此可判斷機(jī)床各加工方向的剛性強(qiáng)弱,以此作為機(jī)床性能改進(jìn)的一種手段,圖4為機(jī)床x向施力圖及變形。
表1的計(jì)算數(shù)據(jù)表明:X/Y/Z 3個(gè)加工方向的剛度分別為189N/um、379N/um、510N/um,可見(jiàn)該機(jī)床最低剛度在戈坐標(biāo)方向,最高剛度在z坐標(biāo)方向。若要對(duì)機(jī)床進(jìn)行剛性加強(qiáng),首選目標(biāo)是加強(qiáng)X方向的剛性。
3、深孔鉆機(jī)床的模態(tài)計(jì)算
模態(tài)分析的目的是通過(guò)計(jì)算固有頻率和振型對(duì)結(jié)構(gòu)設(shè)計(jì)提供參考,當(dāng)激振力頻率接近某一固有頻率時(shí),結(jié)構(gòu)將發(fā)生共振。因此若激振力頻率不可改變,只有通過(guò)改變?cè)O(shè)計(jì)使結(jié)構(gòu)固有頻率避開(kāi)激振頻率。
固有頻率與振型代表結(jié)構(gòu)的內(nèi)在本質(zhì)特性,計(jì)算結(jié)果與邊界條件定義有關(guān),與外力無(wú)關(guān)陋J。為加快計(jì)算速度,一般需要對(duì)分析模型進(jìn)行大量的簡(jiǎn)化,處理過(guò)程需要豐富的分析經(jīng)驗(yàn)。加工過(guò)程中機(jī)床部件之間都存在位置間的相對(duì)運(yùn)動(dòng),對(duì)于某一感興趣的位置進(jìn)行靜力分析時(shí),通過(guò)對(duì)運(yùn)動(dòng)部件間接觸表面施加有限節(jié)點(diǎn)的位移耦合建立邊界條件來(lái)分析,這樣做不會(huì)影響靜力分析結(jié)果的準(zhǔn)確性,因?yàn)殪o力分析中接觸面間的相對(duì)滑動(dòng)只是增加部件間的剛體位移,對(duì)變形和應(yīng)力值沒(méi)有影響。
4、主軸系統(tǒng)處于Y向不同加工位置對(duì)機(jī)床性能的影響分析
機(jī)床主軸沿高度方向處于不同的加工位置時(shí),機(jī)床性能可能有較大差別,如表3所示。圖6為主軸沿y坐標(biāo)從上往下所處的3個(gè)加工位置,從靜力和動(dòng)態(tài)計(jì)算角度分析各加工位置機(jī)床性能。
可見(jiàn),隨著機(jī)床加工位置的變化,機(jī)床性能指標(biāo)也有很大變化。當(dāng)主軸在深孔鉆床立柱底部加工時(shí),機(jī)床動(dòng)態(tài)和靜態(tài)性能最好,機(jī)床剛度是主軸處于頂部時(shí)的3倍左右,頻率值也提高很多。因此當(dāng)加工葉片時(shí)盡量安排在立柱底部進(jìn)行。
5、結(jié)束語(yǔ)
對(duì)回轉(zhuǎn)工作臺(tái)數(shù)控五軸聯(lián)動(dòng)機(jī)床進(jìn)行有限元分析,過(guò)程包括幾何模型簡(jiǎn)化處理、焊接結(jié)構(gòu)零件的板殼結(jié)構(gòu)參數(shù)化、結(jié)合面約束方式等建立有限元模型關(guān)鍵技術(shù),并對(duì)整機(jī)進(jìn)行靜力學(xué)、動(dòng)力學(xué)結(jié)構(gòu)計(jì)算。
(1)靜力下的剛度計(jì)算數(shù)據(jù)表明:X、Y、Z3個(gè)加工方向,最低剛度在x坐標(biāo)方向,數(shù)值為189N/um;最高剛度在z坐標(biāo)方向,數(shù)值為510N/um。該機(jī)床沿x方向剛度最低,若要對(duì)機(jī)床進(jìn)行剛性方面加強(qiáng),首選目標(biāo)是加強(qiáng)該方向的剛性,如可采用加厚立板的方式加強(qiáng)剛性。
(2)模態(tài)計(jì)算結(jié)果表明,機(jī)床初階頻率為41.128Hz,振型沿立柱x方向,證明該方向?yàn)闄C(jī)床最低剛度方向,該結(jié)論與靜力下的計(jì)算結(jié)果完全一致。因此模態(tài)分析結(jié)果對(duì)提高機(jī)床的動(dòng)態(tài)、靜態(tài)剛度均可提供有益參考。
(3)為研究主軸頭運(yùn)動(dòng)對(duì)機(jī)床性能的影響,分別計(jì)算了主軸頭位于立柱頂部、中部、底部3個(gè)位置時(shí),自重下機(jī)床的變形規(guī)律。研究表明,主軸頭位于頂部時(shí)機(jī)床變形最大、剛度最低、初階固有頻率最低?梢(jiàn),隨著機(jī)床加工位置的變化,機(jī)床性能指標(biāo)也有很大變化。當(dāng)主軸在立柱底部加工時(shí),機(jī)床動(dòng)態(tài)和靜態(tài)性能最好,深孔鉆機(jī)床剛度是主軸處于頂部時(shí)的3倍左右,頻率值也提高很多。
1、有限元模型建立
根據(jù)機(jī)床各大件結(jié)構(gòu)情況,采用殼結(jié)構(gòu)(Shell model)和實(shí)體結(jié)構(gòu)(Solid model)混合建模方式建立整機(jī)的有限元模型,對(duì)機(jī)床進(jìn)行結(jié)構(gòu)靜力學(xué)和動(dòng)力學(xué)計(jì)算[410 CAE建模過(guò)程完全采用ANSYS命令流控制,這樣既可以提高計(jì)算精度,同時(shí)又能采用批處理方式處理多種分析工況,提高工作效率。立柱和底座是由薄板焊接成的結(jié)構(gòu)件,所以在有限元建模時(shí)用二維板殼單元建模;主軸頭為復(fù)雜的鑄造結(jié)構(gòu)件,采用三維實(shí)體單元處理。為提高計(jì)算精度,在需要建立位移協(xié)調(diào)關(guān)系的導(dǎo)軌接觸部位的實(shí)體部分用六面體單元?jiǎng)澐志W(wǎng)格,圖1為參數(shù)化后的立柱殼結(jié)構(gòu)模型與有限元網(wǎng)格。
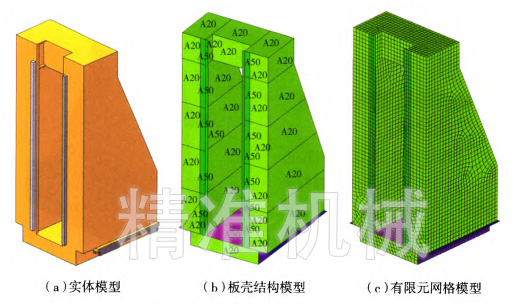
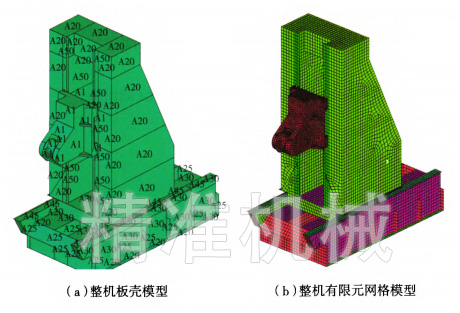
ANSYS提供APDL(ANSYS Parametric Design Language)命令流編程方式編寫分析文件,借助APDL,可實(shí)現(xiàn)結(jié)構(gòu)快速建模、參數(shù)化批量化有限元計(jì)算;并適應(yīng)結(jié)構(gòu)的變化,通過(guò)修改其中的參數(shù),快速生成新的結(jié)構(gòu),之后進(jìn)行網(wǎng)格劃分、加載、求解,完成結(jié)構(gòu)的再分析,通過(guò)綜合比較這些方案的分析結(jié)果,就能發(fā)現(xiàn)結(jié)構(gòu)改進(jìn)的方向。如深孔鉆立柱參數(shù)可分為形狀參數(shù)和厚度參數(shù),形狀參數(shù)定義了結(jié)構(gòu)的拓?fù)渫庥^,厚度參數(shù)用來(lái)給面單元賦值。圖3為通過(guò)參數(shù)輸入建立的3種立柱模型。
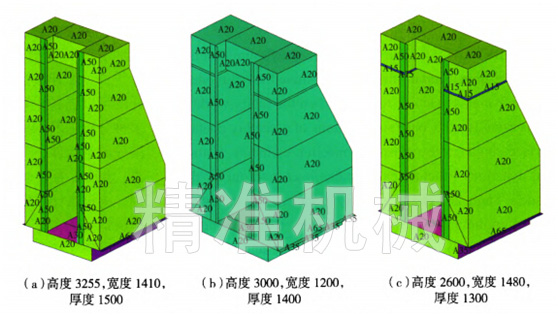
2、機(jī)床靜載荷條件下的性能分析
計(jì)算采用4種工況進(jìn)行,沿x、y、z三加工方向分別施加最大推力,定義為工況l、2、3;最后三方向綜合施加最大推力,定義為工況4。應(yīng)用工況1、2、3的
計(jì)算結(jié)果,可計(jì)算出機(jī)床沿x、y、z各加工方向的剛度,由此可判斷機(jī)床各加工方向的剛性強(qiáng)弱,以此作為機(jī)床性能改進(jìn)的一種手段,圖4為機(jī)床x向施力圖及變形。
表1的計(jì)算數(shù)據(jù)表明:X/Y/Z 3個(gè)加工方向的剛度分別為189N/um、379N/um、510N/um,可見(jiàn)該機(jī)床最低剛度在戈坐標(biāo)方向,最高剛度在z坐標(biāo)方向。若要對(duì)機(jī)床進(jìn)行剛性加強(qiáng),首選目標(biāo)是加強(qiáng)X方向的剛性。
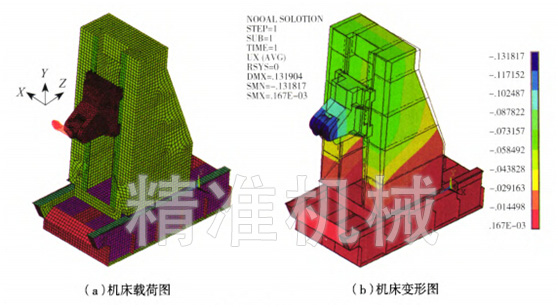
模態(tài)分析的目的是通過(guò)計(jì)算固有頻率和振型對(duì)結(jié)構(gòu)設(shè)計(jì)提供參考,當(dāng)激振力頻率接近某一固有頻率時(shí),結(jié)構(gòu)將發(fā)生共振。因此若激振力頻率不可改變,只有通過(guò)改變?cè)O(shè)計(jì)使結(jié)構(gòu)固有頻率避開(kāi)激振頻率。
固有頻率與振型代表結(jié)構(gòu)的內(nèi)在本質(zhì)特性,計(jì)算結(jié)果與邊界條件定義有關(guān),與外力無(wú)關(guān)陋J。為加快計(jì)算速度,一般需要對(duì)分析模型進(jìn)行大量的簡(jiǎn)化,處理過(guò)程需要豐富的分析經(jīng)驗(yàn)。加工過(guò)程中機(jī)床部件之間都存在位置間的相對(duì)運(yùn)動(dòng),對(duì)于某一感興趣的位置進(jìn)行靜力分析時(shí),通過(guò)對(duì)運(yùn)動(dòng)部件間接觸表面施加有限節(jié)點(diǎn)的位移耦合建立邊界條件來(lái)分析,這樣做不會(huì)影響靜力分析結(jié)果的準(zhǔn)確性,因?yàn)殪o力分析中接觸面間的相對(duì)滑動(dòng)只是增加部件間的剛體位移,對(duì)變形和應(yīng)力值沒(méi)有影響。
4、主軸系統(tǒng)處于Y向不同加工位置對(duì)機(jī)床性能的影響分析
機(jī)床主軸沿高度方向處于不同的加工位置時(shí),機(jī)床性能可能有較大差別,如表3所示。圖6為主軸沿y坐標(biāo)從上往下所處的3個(gè)加工位置,從靜力和動(dòng)態(tài)計(jì)算角度分析各加工位置機(jī)床性能。
可見(jiàn),隨著機(jī)床加工位置的變化,機(jī)床性能指標(biāo)也有很大變化。當(dāng)主軸在深孔鉆床立柱底部加工時(shí),機(jī)床動(dòng)態(tài)和靜態(tài)性能最好,機(jī)床剛度是主軸處于頂部時(shí)的3倍左右,頻率值也提高很多。因此當(dāng)加工葉片時(shí)盡量安排在立柱底部進(jìn)行。
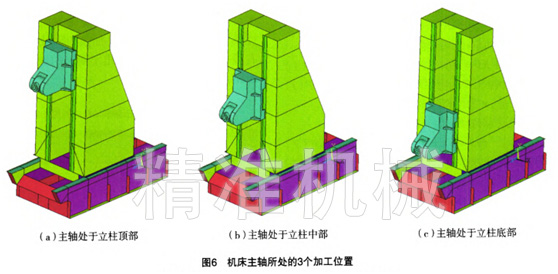

對(duì)回轉(zhuǎn)工作臺(tái)數(shù)控五軸聯(lián)動(dòng)機(jī)床進(jìn)行有限元分析,過(guò)程包括幾何模型簡(jiǎn)化處理、焊接結(jié)構(gòu)零件的板殼結(jié)構(gòu)參數(shù)化、結(jié)合面約束方式等建立有限元模型關(guān)鍵技術(shù),并對(duì)整機(jī)進(jìn)行靜力學(xué)、動(dòng)力學(xué)結(jié)構(gòu)計(jì)算。
(1)靜力下的剛度計(jì)算數(shù)據(jù)表明:X、Y、Z3個(gè)加工方向,最低剛度在x坐標(biāo)方向,數(shù)值為189N/um;最高剛度在z坐標(biāo)方向,數(shù)值為510N/um。該機(jī)床沿x方向剛度最低,若要對(duì)機(jī)床進(jìn)行剛性方面加強(qiáng),首選目標(biāo)是加強(qiáng)該方向的剛性,如可采用加厚立板的方式加強(qiáng)剛性。
(2)模態(tài)計(jì)算結(jié)果表明,機(jī)床初階頻率為41.128Hz,振型沿立柱x方向,證明該方向?yàn)闄C(jī)床最低剛度方向,該結(jié)論與靜力下的計(jì)算結(jié)果完全一致。因此模態(tài)分析結(jié)果對(duì)提高機(jī)床的動(dòng)態(tài)、靜態(tài)剛度均可提供有益參考。
(3)為研究主軸頭運(yùn)動(dòng)對(duì)機(jī)床性能的影響,分別計(jì)算了主軸頭位于立柱頂部、中部、底部3個(gè)位置時(shí),自重下機(jī)床的變形規(guī)律。研究表明,主軸頭位于頂部時(shí)機(jī)床變形最大、剛度最低、初階固有頻率最低?梢(jiàn),隨著機(jī)床加工位置的變化,機(jī)床性能指標(biāo)也有很大變化。當(dāng)主軸在立柱底部加工時(shí),機(jī)床動(dòng)態(tài)和靜態(tài)性能最好,深孔鉆機(jī)床剛度是主軸處于頂部時(shí)的3倍左右,頻率值也提高很多。